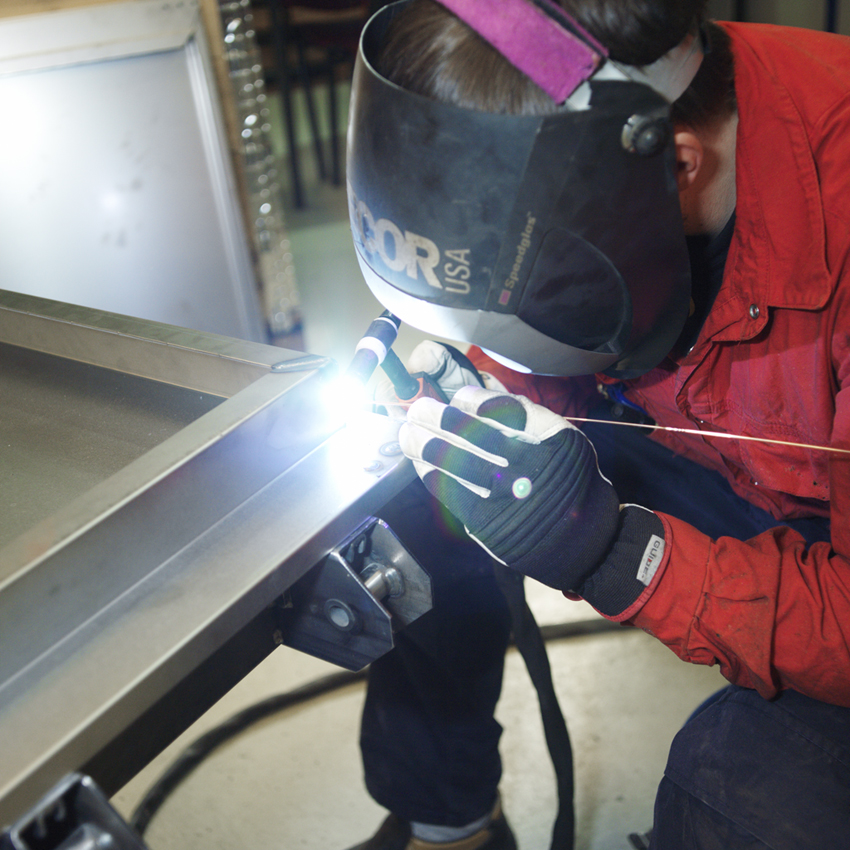
Our modern factory in Bollnäs
was built completely from scratch during 2006 and was opened in January 2007. The total production area is approx. 2300 square metres. It is primarily occupied by our unique filling plant, where we mix and fill our cabinets with the insulation material that allows the filing cabinets to protect documents during fire or to ensure that our fire resistant display cabinets prevent flammable products from igniting. Apart from the filling plant, there are also stores for parts and sheet metal, workplaces for welding and assembly/final assembly.
Before a fire-rated filing cabinet can leave the factory for delivery to your office/workplace, the product passes a number of stations that we summarise in 5 different steps. Sheet Metal, Welding and assembly, Paint, Filling, Assembly.
Bending and punching of sheet metal
is carried out today by our supplier, Weland AB in Smålandstenar. They use their most modern machinery to bend and punch all the parts for our fireproof filing cabinets, fire resistant display cabinets as well as burglary-resistance rated tobacco cabinets, which are then delivered in batches to our factory in Bollnäs.
In the picture, a 2-metre long door plate for the SA 580 is being folded in an ultramodern Salvagnini machine. The entire door is formed from one single piece of 1 mm sheet metal, which places very high demands on the technology and the equipment.
Read more about Weland AB here….


Welding of doors and frame
Doors and frames are produced separately all the way up to when we finally assemble and customise the cabinets. For this to be possible, all the doors and frames for each model must be identical. We solve this thanks to both the precision of the bending above and, above all, because we always use jigs during assembly and welding. Using jigs involves securing the sheet metal in a template that is always identical and then welding, making all the doors and all the frames identical.
This gives us opportunity for faster manufacturing and, in addition, allows us later to replace a door on a fire-rated filing cabinet that has, for example, been damaged during transport or removal etc., which could otherwise be difficult.
Joining internal and external frames
To provide the maximum fire protection, we have a unique solution for joining the internal frame with the external one, giving us excellent protection in the frame. The external sheet metal (which is exposed to direct heat during a fire) only meets the internal frame at the front edge, via an aluminium strip that, moreover, is placed protected behind the doors. In other words, there is no contact between the external metal and the internal metal (inside the cabinet) at the back, sides, bottom or top, instead, where the metal is completely free and is only in contact with our fire insulation. We use the same frame for our fire-rated filing cabinets for our fire resistant display cabinets as well, which means that the SGS series, in particular, has a much higher level of protection than the SP2369 test actually demands.


Powder coating
All of the parts for our fire-rated filing cabinets and fire resistant display cabinets are painted by our subcontractor, Kesam AB. Our factories are neighbours, with direct access via an internal entrance, meaning we do not need to transport the cabinets to get them painted.
The proximity of Kesam also gives us another advantage when it comes to, for example, other contract work, where our expertise lies in design, welding and assembly, while Kesam’s expertise is everything and anything to do with painting.
Read more about Kesam AB here….
Preparation prior to filling
To guarantee that nothing twists while we are filling the frames with fire insulation, all of the cabinets are first secured. We call this preparation and, in brief, involves us securing the walls internally and the opening where the doors will be fitted. When fixing the door hole, a solid panel with the same piston positions as the doors (see illustration) is used, which further guarantees the fit. Afterwards, we lay the frames down front first on trolleys and secure them in magazines of 10-12 cabinets per trolley.
Because we use the same frame for both our fireproof filing cabinets and our fire resistant cabinets, the procedure is the same for both series.


Filling with fire insulation
The fire insulation, which consists of a special concrete mixed in a separate mixer, which is then pumped out via hoses to the trolleys where the cabinets are secured. Our unique filling technology, means we prevent dust and dirt, which is otherwise a major problem when handling concrete.
We use the same filling technology for both our fireproof filing cabinets and our fire resistant display cabinets.
Assembly / customised
When the concrete has hardened, we lift the frames up directly on to pallets and they are readied for intermediate storage. The same is true for all of the doors that are filled with fire insulation. They lie in our door store, where we have room for more than 300 doors at any one time. From here on in, everything is controlled by the customer so, when we receive orders for different models of cabinet, we take out the right frame and door, fit the selected lock and fittings and pack the cabinets for safe transport to the customer.
Our manufacturing procedure means we can deliver entirely customised filing cabinets and fire resistant cabinets at short notice.


Delivery to you!
When the filing cabinet is packed, it is dispatched either via Schenker or Posten Logistik to one of our partners in Sweden or Scandinavia who is specialised in the safe reception of heavy goods or, alternatively, straight to you, if you choose to receive the cabinet at the office/shop or similar.
The fire resistant cabinets are reasonably easy to put in place yourself, while we recommend that you make use of our transport procedure, with reception at indicated location, for the SA series.